Introduce some maintenance experience of single-stage BWD6-35-30KW cycloidal pinwheel reducer
Here are some maintenance experiences for single-stage BWD6-35-30KW cycloidal pinwheel reducers:Pre maintenance inspection
Appearance inspection: Check for cracks or damage to the gearbox casing, loose bolts at all connection points, and any signs of oil leakage.
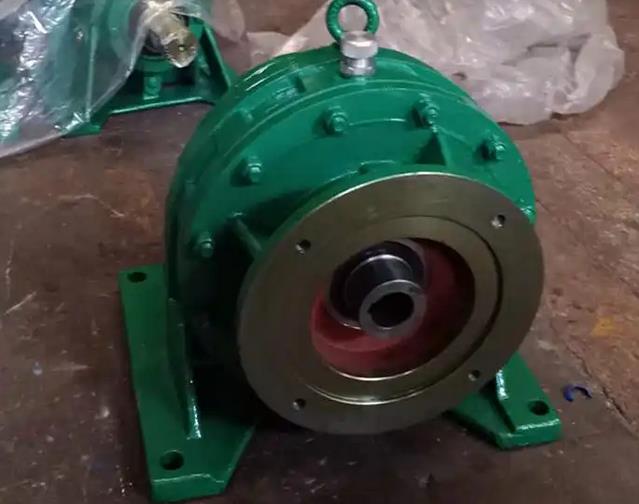
Operation inspection: Before stopping the machine, observe whether there is any abnormal vibration or noise during the operation of the gearbox, whether the temperature is too high, and whether the transmission is smooth. At the same time, check the load condition of the gearbox to ensure that it operates within the rated load range.
Oil level and quality inspection: Check the lubricating oil level through an oil level gauge to ensure that the oil level is within the normal range. If the oil level is too low, it is necessary to search for any oil leakage points. Observe the oil quality. If the oil color turns black or turbid, or there are obvious impurities such as metal shavings, the lubricating oil should be replaced in a timely manner.
Common fault maintenance
Oil leakage: If the oil seal is aging or damaged, it needs to be replaced. When installing a new oil seal, pay attention to the installation direction and position to ensure a tight fit between the oil seal and the shaft surface. If there is oil leakage due to the failure of the sealant on the joint surface of the box, the joint surface can be cleaned and the sealant can be reapplied. In addition, check if the oil level is too high to avoid oil leakage caused by high oil level.
Bearing damage: Bearing damage can cause abnormal noise and vibration. When repairing, it is necessary to disassemble the gearbox, remove the damaged bearings, record the model and specifications of the bearings, and replace them with new ones. When installing bearings, use appropriate tools to ensure proper installation and avoid installing the bearings too tightly or too loosely. At the same time, check whether the bearing seat is worn, and if it is worn, repair or replace it.
Gear wear: Severe gear wear can affect the transmission efficiency and accuracy of the gearbox. When gear wear is found, it is necessary to decide whether to replace the gear based on the degree of wear. If the gears are only slightly worn, the transmission performance can be improved by adjusting the meshing clearance of the gears. When installing new gears, ensure the installation accuracy of the gears and ensure good meshing between the gears.
Cross axis fault: Cross axis may be caused by broken teeth causing the input shaft to lose axial restraint, or by the driven gear on the intermediate shaft not being securely fastened to the shaft. For the problem of broken teeth, the damaged gear needs to be replaced; For situations where the driven gear and shaft are not securely fastened, it is necessary to check whether the interference fit is sufficient. If it is insufficient, relevant components need to be readjusted or replaced to ensure a firm connection between the gear and shaft.
Commissioning after maintenance
No load debugging: After the maintenance is completed, conduct a no-load trial run first. Start the reducer and observe whether it runs smoothly, whether there is any abnormal noise or vibration, and check whether there is any looseness in the connecting parts. At the same time, check whether the oil temperature and level are normal, and whether there is any oil leakage at the oil seal.
Load debugging: After the no-load debugging is normal, perform load debugging. Gradually increase the load, observe the operation of the gearbox under different loads, and check whether its transmission efficiency, temperature changes, vibration, and noise meet the requirements. During the load debugging process, it is necessary to closely monitor the various operating parameters of the gearbox. If there are any abnormalities, the machine should be stopped and checked in a timely manner. After troubleshooting, the debugging can continue.