What is the difference between gear grinding process and gear shaving process for reducers
Gear grinding process and gear shaving process are two commonly used processes in gear machining. They have some differences in machining principles, machining accuracy, machining efficiency, equipment cost, etc., as follows:processing principle
Grinding process: Using a grinding wheel as a grinding tool, the tooth surface is ground by the relative motion between the grinding wheel and the gear tooth surface, in order to remove the excess of the tooth surface and achieve th
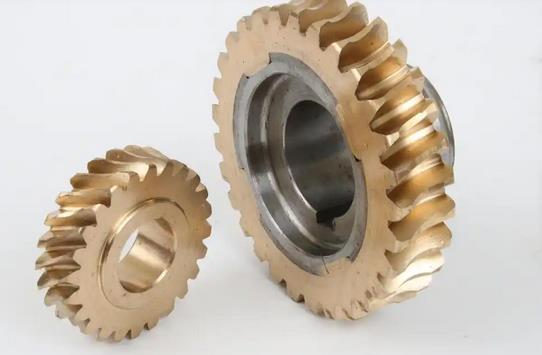
Machining accuracy
Grinding process: It can achieve high machining accuracy, generally reaching IT5-IT6 level accuracy, or even higher. Grinding teeth can effectively correct the deformation of gears during heat treatment, with precise control over tooth shape and orientation, and is suitable for high-precision gear machining.
Shaving process: The machining accuracy is usually around IT6-IT7 level. Although shaving teeth can also improve the accuracy of gears, it may not fully meet the accuracy requirements for some high-precision gears. However, in some situations where precision requirements are not extremely high, the precision of the shaving process can already meet the usage requirements.
processing efficiency
Grinding process: Due to the large contact area between the grinding wheel and the tooth surface during grinding, the grinding force and heat are high. In order to ensure the machining quality and the service life of the grinding wheel, the feed rate of the grinding wheel is usually small, the machining speed is relatively slow, and the machining efficiency is low. Especially for large module and large-sized gears, the machining time for grinding teeth will be longer.
Shaving process: The shaving cutter and gear are in line contact cutting, with low cutting force, high cutting speed, and large feed rate, resulting in high machining efficiency. The shaving process is suitable for efficient precision machining of gears in mass production, and can complete a large number of gear machining in a relatively short time.
Equipment cost
Grinding process: The structure of the grinding machine is complex, with high precision requirements and expensive equipment prices. At the same time, specialized grinding wheels are required during the gear grinding process, and the replacement and repair of the grinding wheels also require certain costs and time. Therefore, the equipment and processing costs of the gear grinding process are relatively high.
Shaving process: The structure of the shaving machine is relatively simple, and the equipment price is relatively low. The service life of a shaving cutter is relatively long, the frequency of replacement is relatively low, and the processing cost is also relatively low. However, the manufacturing accuracy requirements for gear cutters are high, and their procurement costs cannot be ignored.
scope of application
Grinding process: suitable for various types of gear machining, especially for hard tooth gears with high precision requirements, aerospace gears, high-speed heavy-duty gears, etc. Grinding is an important precision machining method for gears that have undergone quenching and other heat treatments, which can eliminate heat treatment deformation and ensure the accuracy and performance of the gears.