How to diagnose abnormal noise in Siemens gearbox during operation
Abnormal noise occurs during the operation of Siemens reducers, which may be caused by problems with gears, bearings, motors, loads, etc. The following are specific diagnostic methods:Gear problem
Check the wear of gears: After long-term operation, gears may experience wear, pitting, peeling, and other phenomena on the tooth surface, which can lead to a decrease in meshing accuracy and produce abnormal noise. The degree of gear wear can be evaluated by observing the wear marks on the surface of the gear and measuring the tooth thickness. For gears with severe wear, they need to be replaced in a timely manner.
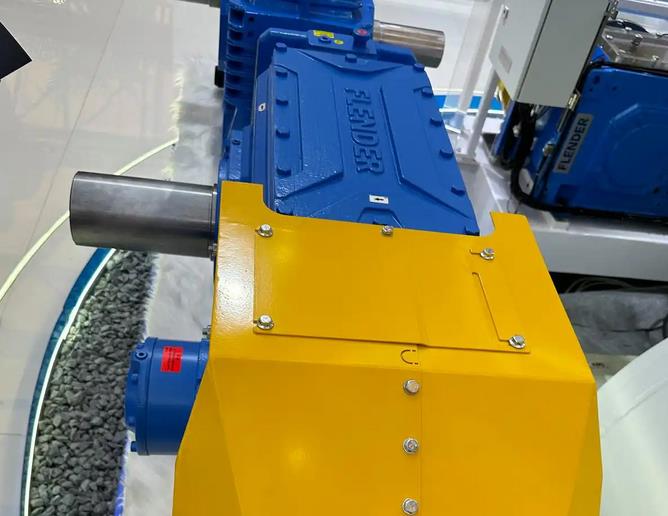
Check the gear meshing condition: Incorrect gear meshing, such as excessive or insufficient meshing clearance, poor contact between meshing surfaces, etc., can also cause noise. You can use a feeler gauge to measure the gear mesh clearance and check if it is within the specified range. At the same time, by applying paint on the tooth surface and allowing the gear to rotate, observe the paint imprint on the tooth surface to determine the contact condition of the meshing surface. If the meshing condition is poor, it is necessary to adjust the installation position of the gear or perform tooth profile adjustment.
Bearing issues
Check for bearing wear and damage: Bearing wear or damage can cause unstable operation and generate noise. You can make a preliminary judgment by listening to the sound. If you hear a sound similar to "gurgling", it may be a problem with the bearing. Further, a vibration tester can be used to detect the vibration of the bearing. If the vibration value exceeds the normal range, it indicates that the bearing may have a fault. In addition, the clearance of the bearings can also be checked. If the clearance is too large, it will also affect the normal operation of the gearbox. Damaged bearings should be replaced promptly.
Check the lubrication condition of the bearings: Good lubrication is the key to ensuring the normal operation of the bearings. If the amount of lubricating oil is insufficient, the oil quality deteriorates, or the lubrication method is improper, it may lead to bearing overheating, increased wear, and noise generation. Check whether the lubricating oil level is within the normal range, whether the oil quality is good (which can be judged by observing the color, viscosity, and impurities of the oil), and confirm whether the lubrication system is working properly, such as whether the oil nozzle is blocked and whether the oil pump is supplying oil normally.
Motor issues
Check for motor imbalance: Motor imbalance can cause vibration and noise in the gearbox. A dynamic balance meter can be used to detect the motor and determine the degree and position of imbalance. For unbalanced motors, dynamic balance correction is required to reduce vibration and noise.
Check for motor winding faults: Short circuits, open circuits, or grounding faults in the motor winding can cause abnormal motor operation and produce abnormal noise. Use an insulation resistance tester to measure the insulation resistance of the motor winding and check for any insulation damage. At the same time, it is possible to determine whether there is a short circuit in the winding by detecting the current of the motor. If the current of a certain phase increases abnormally, there may be a short circuit fault in the winding of that phase. For winding faults, it is necessary to repair or replace the motor.