What are the common faults of the output shaft and input shaft of the reducer
The common faults of the output shaft and input shaft of the reducer are as follows:wear and tear
Gear wear: Gears are critical components that are connected to the shaft and transmit power, and can operate for extended periods of time
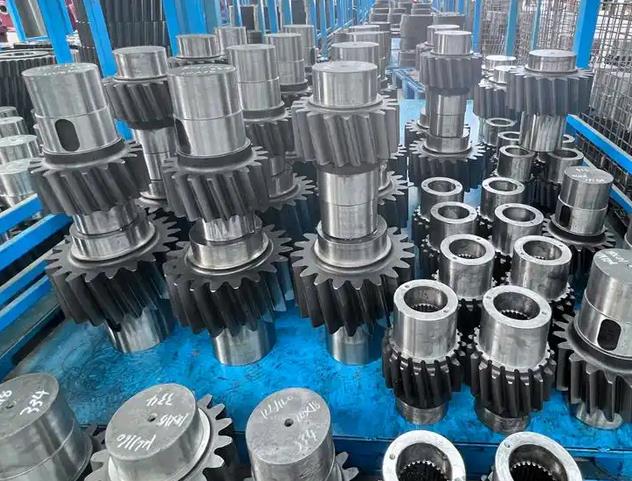
After driving, the tooth surface will experience wear due to friction, fatigue, and other factors, resulting in changes in tooth profile and an increase in tooth side clearance, which affects transmission accuracy and efficiency. The gears on the input shaft often experience accelerated wear due to frequent starting and braking, which can result in significant impact loads; The output shaft gear may wear out due to long-term heavy load.
Journal wear: The journal is the part where the shaft and bearing fit together. Due to long-term relative motion and load, the surface of the journal will wear, resulting in an increase in fit clearance and affecting the positioning accuracy and stability of the shaft. The output shaft neck may experience more severe wear due to greater radial and axial forces.
deformation
Bending deformation: When the bending moment borne by the shaft exceeds its bearing capacity, bending deformation occurs. It may be caused by misalignment during installation, additional bending moments due to poor gear meshing, or excessive external loads. When the input shaft is transmitting power, if the motor is not installed firmly or the coupling is not aligned, it is easy to cause bending deformation; If the working mechanism connected to the output shaft has a large eccentric force, it will also bend.
Twisted deformation: If the torque borne by the shaft exceeds the material's torsional strength, torsional deformation will occur. Usually caused by overload operation of the gearbox, or excessive impact torque generated during starting and braking processes. The input shaft may experience significant impact torque at the moment of start-up, and if it exceeds its bearing capacity, torsional deformation may occur.
fracture
Fatigue fracture: Under long-term alternating loads, the shaft will produce fatigue cracks in stress concentrated areas such as key slots, shaft shoulders, transition corners, etc. As the cracks propagate, they will ultimately lead to the fracture of the shaft. Due to frequent starting and braking, the input shaft is subjected to high alternating stress and is more prone to fatigue fracture.
Overload fracture: When the load borne by the reducer exceeds the ultimate bearing capacity of the shaft, it will cause sudden fracture of the shaft. This may be due to factors such as the working mechanism getting stuck or unexpected impacts, causing the shaft to bear forces far beyond the design load. The output shaft may experience overload fracture when driving large loads or encountering sudden large resistance.
Key connection failure
Key wear: Keys are important components that connect shafts, gears, couplings, and other transmission parts. During the transmission of torque, friction occurs between keys and keyways. After prolonged use, keys may wear out, causing loose fit between keys and keyways and affecting the reliability of power transmission.
Key fracture: When the shear or compression force on a key exceeds its strength limit, it will break. This may be caused by overload, poor material quality of the key, or insufficient machining accuracy of the keyway.
bearing failure
Bearing wear: Bearings are the components that support the rotation of the shaft. After long-term operation, the rolling elements and raceways of bearings will wear due to friction, fatigue, etc., resulting in increased clearance, decreased rotational accuracy, vibration, and noise. The bearings of both the input and output shafts may experience accelerated wear due to poor lubrication, excessive load, improper installation, and other reasons.